1.FMEA培训时间
1月18-19日,3月27-28日,4月29-30日,5月21-22日,6月28-29日,7月19-21日,8月27-28日,9月21-22日,10月28-29日,11月21-22日,12月12-13日
2.FMEA培训地点
公开课程地点:杭州、上海、北京、广州、成都、南京、苏州每月滚动开班。
3.FMEA培训费用
课程费用:3,200RMB/人,3人以上团体报名9.5折优惠。
4.FMEA培训报名
5.FMEA培训目标
研究AIAG VDA FMEA和第4版之间的变化和差异。如何使两种方法的结果相同?
详细说明AIAG VDA设计和FMEA实现的最佳方法。
将DFMEA与DVPR连接并使用预防检查表
链接SFMEA、DFMEA、工艺流程、PFMEA和控制计划
了解如何将DFMEA与故障、保修历史和质量低劣的成本(COPQ)联系起来
掌握《AIAG-VDA FMEA软件使用》,了解软件在AIAG-VDA FMEA中的作用。
实施AIAG-VDA和其他供应链标准
使用AIAG-VDA DFMEA检查表评估完成,并在应用DFMEA时提供一致性。
制定AIAG-VDA DFMEA过渡和实施计划。
6.FMEA培训对象
质量体系推行人员
工程技术人员
质量体系内审员
任何参与产品工程、制造、质量控制,或销售的相关人员
任何需要学习质量体系管理工具的人员
7.FMEA培训特色
强了解最新版(第一版)FMEA的背景及主要变化点;
掌握和理解失效模式和后果分析(FMEA)概念、信息流、七步法
通过方块图/界限图,正确界定FMEA的范围;
应用结构图,分析零件与零件之间在物体、能量、信息、物质形态方面的交互作用;
8.培前准备(如内训)
分组:
每组人数:请将参加培训的学员按照每组不超过6人的方式分层不同的小组;
成员:每个小组以产品设计工程师为主,其他职能成员均匀分配至各小组(一般常见的其他职能成员包括:质量、制造设计工程师、可靠性工程师等);
小组产品/技术:最好以公司的产品类型作为分组的基础(如组内的产品设计人员都是同一个系列的产品设计人员)
人数超出规定的处理:建议的学员人数总数不超过30人(五组),如果组数超过五组,小组成果分享、培训师对小组练习的辅导会受到影响。如果有超出,培训师会选择性的进行辅导和分享,或者增加培训人天数。
技术资料准备:如涉及保密问题,以下资料不需要提交
产品的技术规格书/产品标准/试验标准清单
设计BOM
售后故障/质量资料(用于失效模式识别)
之前在DFMEA应用方面遇到的问题(在培训前测试中也有相关的提问)
之前内外部审核中遇到的问题(在培训前测试中也有相关的提问)
原有的DFMEA文档
9.FMEA培训大纲
一、失效模式影响分析(FMEA)的描述
1.FMEA的目的、起源、分类和实施原则
2.设计FMEA(DFMEA)的简介、顾客的定义、执行时机
3.FMEA实施步骤模式-七步法图解
步骤一:定义范围;
步骤二:结构分析;
步骤三:功能分析;
步骤四:失效分析;
步骤五:风险评估;
步骤六:措施优化;
步骤七: 风险结果。
二、DFMEA实施准备
1.DFMEA核心小组-跨功能小组的成立
2.PDCA Cycle循环-团队运作
3.DFMEA的开发(功能框图)
三、DFMEA的实施
1)DFMEA顾客的定义说明
2)DFMEA中失效模式与影响的对应关系
3)DFMEA小组的实施步骤-七步法
4)设计框图的制定和分析
5)DFMEA严重度、发生率、侦测度评价准则
6)风险评估 -行动优化级(AP)
7)DFMEA技术分析法则与应用实例解析
四、采取后续改进措施的时机
五、企业产品设计FMEA现场分组演练、分析与总结
六、DFMEA的跟踪
日程
|
题目
|
培训内容
|
开始
|
结束
|
培训时长
|
第1天
|
第1章-失效模式和
–影响分析(FMEA)介绍
|
课程概述和介绍
矿用设备FMEA案例演示
一、FMEA介绍
1、AIAG-VDA FMEA背景及主要变化
2、FMEA目的和描述
3、FMEA开发过程及里程碑
4、FMEA的对象与局限性
5、如何与公司的现况进行整合
l FMEA的法律考量
管理者承诺
FMEA专有技术保护
客户与供应商之间的协议
FMEA的参考
FMEA换版处理
|
9:00
|
10:30
|
1:30
|
课间休息
|
|
10:30
|
10:40
|
0:10
|
第2章 设计FMEA
|
6、产品FMEA与过程FMEA
FMEA的三种应用情况
设计FMEA
过程FMEA
设计FMEA到过程FMEA的信息流
7、FMEA项目计划
FMEA的团队
FMEA时间接点
FMEA意图
FMEA工具
FMEA任务
|
10:40
|
12:00
|
1:20
|
午餐
|
|
12:00
|
13:00
|
1:00
|
|
DFMEA与其它文件间的相互关联(DVP&R)
FMEA的时间节点
FMEA表格的变化
SOD评分的变化
RPN的缺陷
新的风险优先级评估方法AP
|
13:00
|
14:30
|
1:30
|
课间休息
|
|
14:30
|
14:40
|
0:10
|
|
1、DFMEA七步法
2、步骤一:范围定义
l 目的
l 定义范围的内容
课堂练习:1、定义FMEA范围
|
14:40
|
17:00
|
2:20
|
第2天
|
|
3、步骤二:结构分析
目的
系统FMEA
零部件FMEA
定义顾客
产品框图
结构树图
品质机能展开(视需要展开)
案例展示:矿用设备结构树图和边界图
课堂练习:1、产品框图
2、产品结构树
3、DFMEA结构分析
|
9:00
|
10:30
|
1:30
|
课间休息
|
|
10:30
|
10:40
|
0:10
|
|
4、步骤三:功能分析
目的
功能
接口
要求
产品特性
参数图
功能关系的可视化
案例展示:矿用设备功能树图
课堂练习:1、参数图
2、功能关系树
3、DFMEA功能分析
|
10:40
|
12:00
|
1:20
|
午餐
|
|
12:00
|
13:00
|
1:00
|
|
5、步骤四:失效分析
目的
失效的种类
失效链
失效网和失效链分析
失效的影响
失效的模式
失效的原因
总结
案例展示:矿用设备功能常见故障及原因分析
课堂练习:1、制作失效树
2、DFMEA失效分析
|
13:00
|
15:00
|
2:00
|
课间休息
|
|
15:00
|
15:10
|
0:10
|
|
6、步骤五:风险分析
目的
设计控制
现行的预防措施
现行的探测措施
现行预防和控制措施确认
严重度
发生度
探测度
行动优先级
案例展示:矿用设备功能设计控制措施例
课堂练习:1、DFMEA风险分析
|
15:10
|
17:00
|
1:50
|
第3天
|
|
7、步骤六:优化
目的
职责分配
行动的状态
评估行动有效性
持续改进
案例展示:矿用设备功能设计优化例
课堂练习:1、DFMEA优化
8、步骤七:结果报告
|
9:00
|
10:30
|
1:30
|
课件休息
|
|
10:30
|
10:40
|
0:10
|
|
测试计划及报告(DVP&R)
– 设计验证
– 噪音因素
– 测试
案例展示:矿用设备可靠性测试例
|
10:40
|
12:00
|
1:20
|
午餐
|
|
12:00
|
13:00
|
1:00
|
|
一、磨机、提升机、过滤设备DFMEA案例展示如何按照新版本FMEA方法进行DFMEA分析
通过workshop的形式,保证每个组员都能够参与整个FMEA案例分析的流程并提出见解,加深对设计和过程FMEA的理解和运用,还原“真实的”FMEA工作环境。
|
13:00
|
15:00
|
2:00
|
课间休息
|
|
15:00
|
15:10
|
0:10
|
|
三、功能安全硬件分析与指标计算
四、如何应用专业工具实施FMEA
五、答疑(Q&A)
|
15:10
|
16:00
|
0:50
|
考核
|
笔试考核(一般情况下老师根据贵公司产品让学员分组进行DFMEA打分等,若企业有需求,可以进行试卷考试)
|
16:00
|
17:00
|
1:00
|
培训案例:
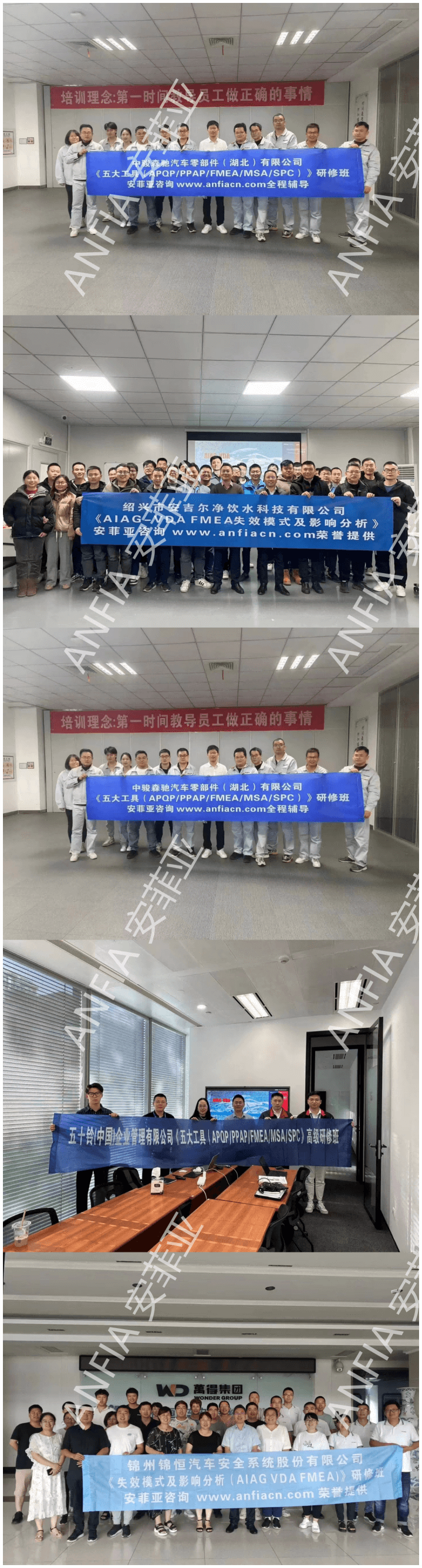
阅读本文的人,还阅读了: